Steel Cans Facts
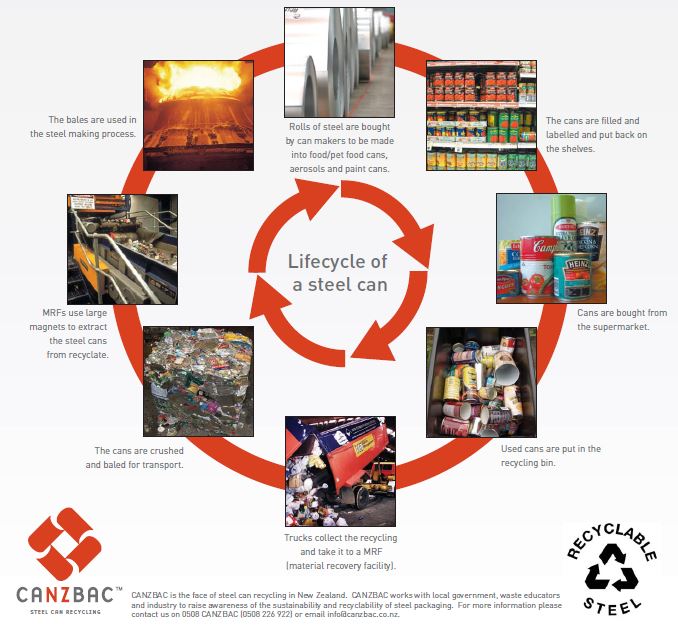
Steel is the world’s most recycled material.
- Steel packaging is used for drink cans, food and petfood cans, paint cans, aerosols and containers of many other household and industrial products.
- The average New Zealand family uses six steel cans per week.
- Steel cans are the easiest type of packaging to recycle as they can be picked out of the garbage and recycling waste by magnetic separation.
- Each steel can is 100% recyclable. It can be recycled over and over again into new products like, bikes and of course new steel cans.
- The steel can was first developed in the early nineteenth century to solve the problem of keeping food fresh for the soldiers in battle.
- Steel cans, often called tin cans, have only a very thin layer of tin - 15 millionths of an inch thick to prevent corrosion – thinner than the skin of a soap bubble.
- Some 2 billion steel cans are recycled on average each year – that’s about seven million cans every working day, enough to make a circle around the world five times.
- Today’s steel can weighs 40% less than it did 30 years ago – saving raw materials and making lighter work of the weekly shopping basket.
- Producing steel from recycled material saves 75% of the energy needed to make steel from virgin material.
- For every tonne of steel cans recycled 1.5 tonnes of iron ore, 0.5 tonnes of coal and 40% of water required in the production process is saved.
The Steel Making Process
Every year the New Zealand steel industry recycles almost one million tonnes of scrap steel from recycled cans, cars, appliances, construction materials and other steel products. This scrap is melted down to produce new steel. Steel cans, including food, paint and aerosol cans, are an important part of the steel recycling loop and were recycled at a rate of approximately 340,000 tonnes in 2004 – which is 53% of all steel cans used.
Recycling is an integral part of the steel making process. Steel mills use one of two types of furnaces to make new steel. Both furnaces recycle old steel products into new steel, but each is used to create different products for varied applications.
The first - the basic oxygen steel making process - uses a maximum of 25% scrap steel to make new steel. This furnace produces the steel used in flat-rolled steel products, such as cans, appliances and automobiles.
The other type of steel making furnace - the electric arc furnace - melts virtually 100% scrap steel to make new steel. This steel is used primarily to make products that are long shapes, like steel plate, rebar and structural beams.
And, since all new steel products contain recycled steel, when you buy steel you help to close the recycling loop by buying recycled!
The Continuous Recycling Loop Of Steel
When you return your used steel cans for recycling, you are helping to ensure that new steel products are made from recycled steel. Steel can be recycled again at the end of their useful lives. Used steel cans are recycled into new steel cans, which may one day be recycled again into an appliance like a fridge or washing machine.
An infrastructure of ferrous scrap processors exists to prepare all types of steel products for recycling. Processors prepare and ship scrap steel to steel mills and foundries for remelting into new steel.
When you realise how useful steel is, it seems a terrible waste to send it to landfill!